Metalens mass production is transforming the optics industry, offering scalable, high-quality solutions for advanced applications in various fields. This article is intended to provide a guideline for customized metalens design and fabrication services. To learn more about the technology and our company, please refer to this. For a detailed comparison of metalenses with traditional optics, read: Metalenses Vs. Traditional DOEs And Refractive Lenses: A Comprehensive Comparison. To explore our available off-the-shelf products, please visit our web store.
If you cannot find what you need from the above resources, you may require a customized solution. Please continue reading for further details.
Technical Capabilities #
Metalens Design Tool: Meta Optics Composer Studio #
We develop our own software for metalens design: Meta Optics Composer Studio, featuring the following unique capabilities:
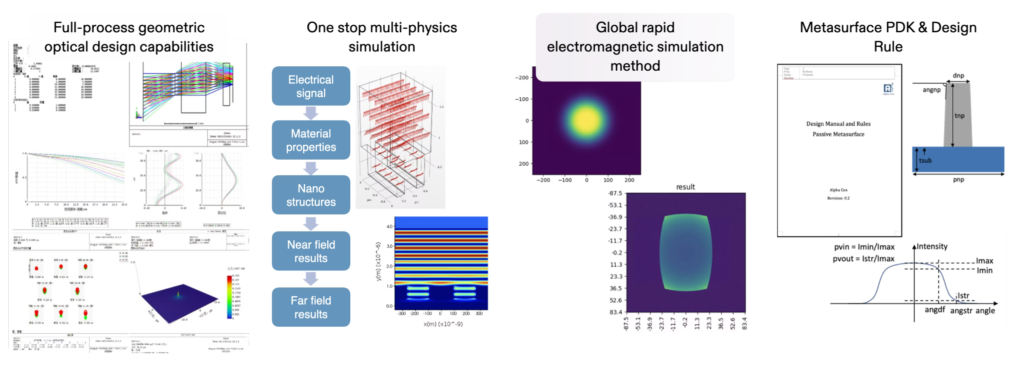
- Geometric optical design
- Interlinked nano-structure and macro performance data
- Global optimization for optimal system performance
- Comprehensive multi-physics simulation
- Multi-physics simulation of complex material systems
- Unique active metasurface design capabilities
- Rapid electromagnetic simulation tool
- Global optimal solution search algorithm
- Support for wide spectrum lens design in the visible range
- Metasurface PDK and design rules
- End-to-end performance control from design to mass production
Metalens Mass Production – CMOS Compatible, Mass Production Proven Foundry #
We co-developed our metalens fabrication process with a standard 12-inch, 55 nm IC foundry, leveraging CMOS processes to achieve consistent, low-cost mass production.
Below is a comparison of different metalens fabrication techniques:
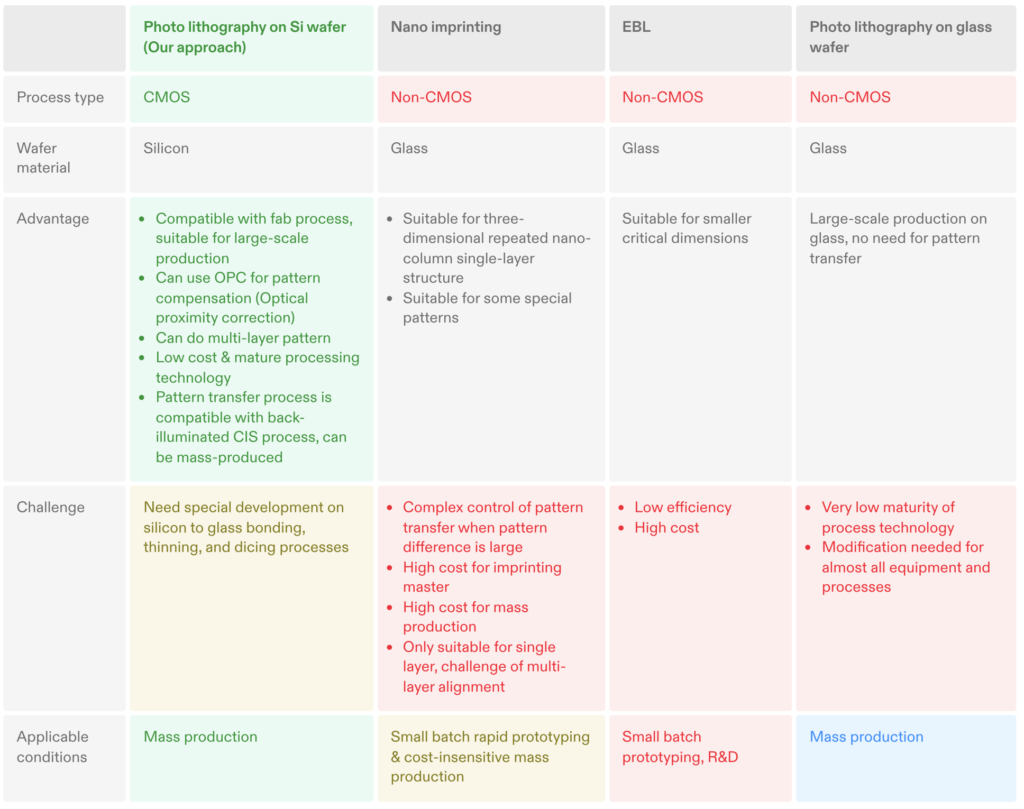
Full Process Technical Capabilities #
We provide full process technical capabilities, including design, manufacturing support, system integration, and application development. Our system integration team members have extensive experience in mass production, and all reference designs meet mass production standards.
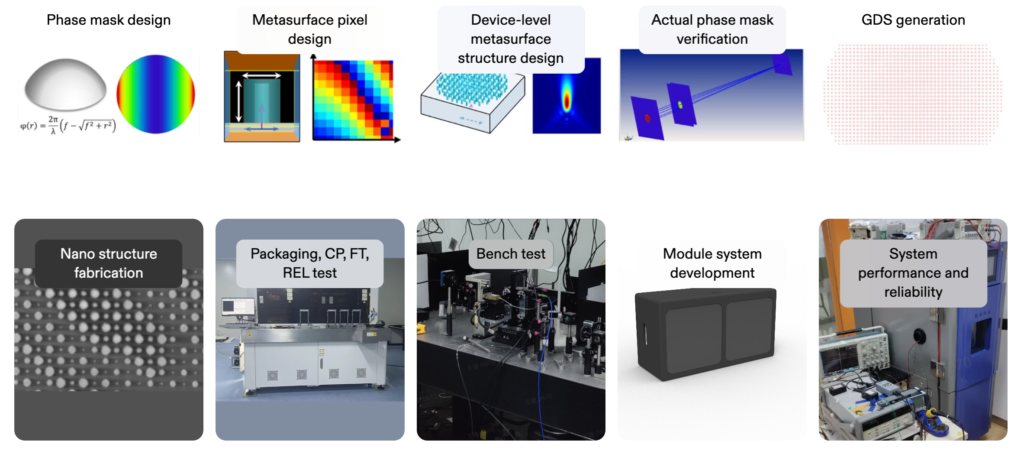
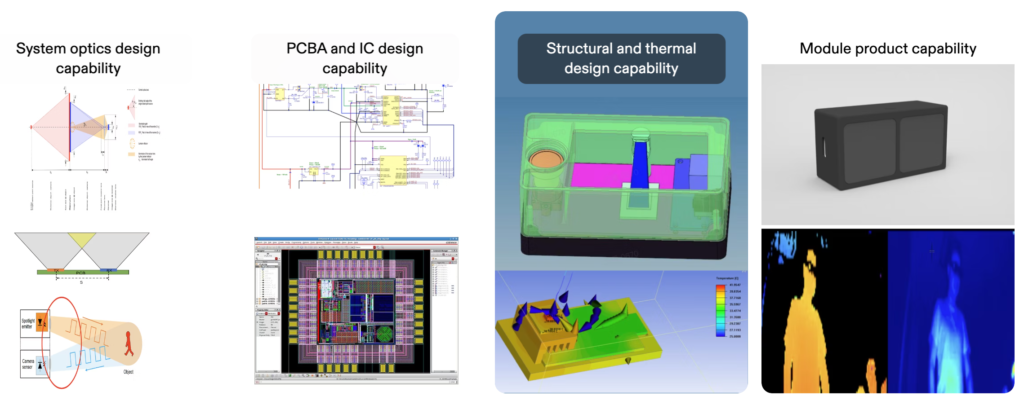
Design Service #
Please submit your request through our custom quotation form. We recommend providing as much information as possible to begin the evaluation. To assist with this, we have prepared a set of Request for Information forms. Please complete one of the forms as needed and attach it to the custom quotation form. If your design requirements differ from those mentioned in the Request for Information forms, please attach your own specifications.
After confirming the specifications, we will conduct a quick feasibility study and provide recommendations and cost estimations.
Pilot Run #
For high-risk or exploratory projects, we offer E-beam lithography prototyping through a partnership with a nanofabrication laboratory. The available equipment and capabilities are listed below:
Equipment Name | Function Description |
Contact Lithography Machine | UV exposure of photoresist, alignment for overlay exposure, supports double-sided overlay |
Optical Coating Machine | Deposition of anti-reflection and reflective coatings for laser end facets/optical elements |
Electron Beam Lithography System | Supports 2/4/6/8-inch wafers and individual pieces, minimum line width of 8nm |
PECVD | Deposition of dielectric films (SiOx, SiNx) |
RIE | Etching of dielectric films (SiOx, SiNx) |
ICP | Etching of Si, III-V materials, lithium niobate, etc. |
Cleaving Machine | Scribing and cleaving of III-V material wafers |
Magnetron Sputtering Coater | Deposition of dense metal films |
Electron Beam Evaporator | Metal film deposition, electrode fabrication |
Dual Beam Electron Microscope | High-precision characterization of surface and cross-sectional structures, elemental analysis, chip failure analysis, TEM sample preparation, metamaterial device fabrication |
Rapid Thermal Annealing Furnace | High-temperature annealing treatment |
Plasma Cleaner | Organic surface cleaning, photoresist removal |
Thinning and Polishing Machine | Wafer thinning and surface polishing |
High Magnification Digital Microscope | Optical microscopy, surface characterization |
Profilometer | Vertical height characterization of step structures |
Film Thickness Measurement Tool | Measurement of thin film thickness |
3D Profilometer | Surface smoothness inspection of wafers |
Semi-Automatic Die Bonder | High-precision chip alignment and bonding |
Small Batch Production #
For small batch production, we use the same process as mass production, but the mask is shared among various projects to keep costs reasonable.
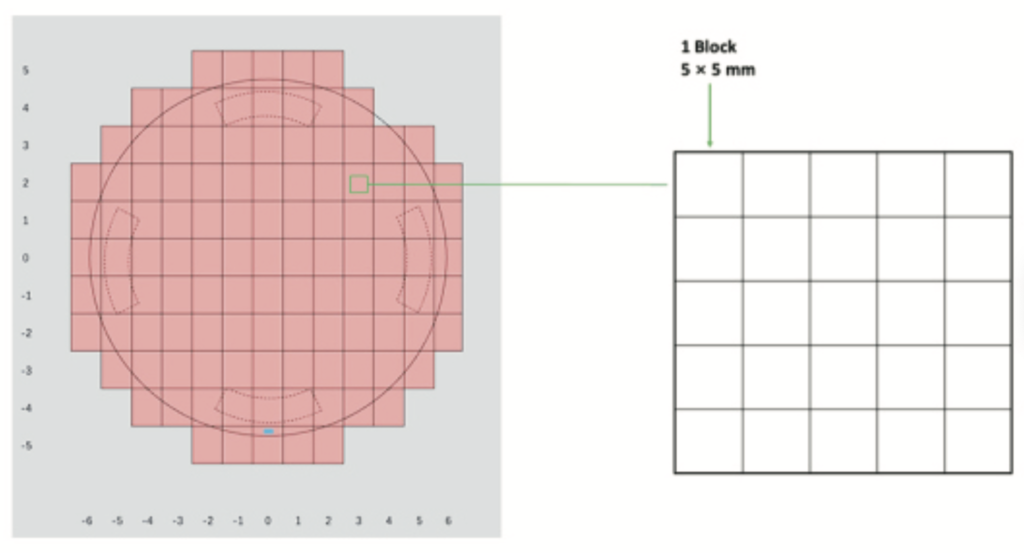
The die size in an MPW project should not exceed 1 Block (5mm x 5mm) to accommodate other projects and meet dicing requirements. Larger sizes incur higher costs due to the inability to share the mask with other projects.
Please contact us for the detailed MPW shuttle schedule. Once the GDS file is confirmed, lead time for MPW samples is typically 10 weeks.
Mass Production #
Mass production requires a new mask with a single die and an engineering lot of 15 wafers for process tuning. The minimum order quantity varies by project but starts at 1 lot (25 wafers).
We currently follow below process for mass production:
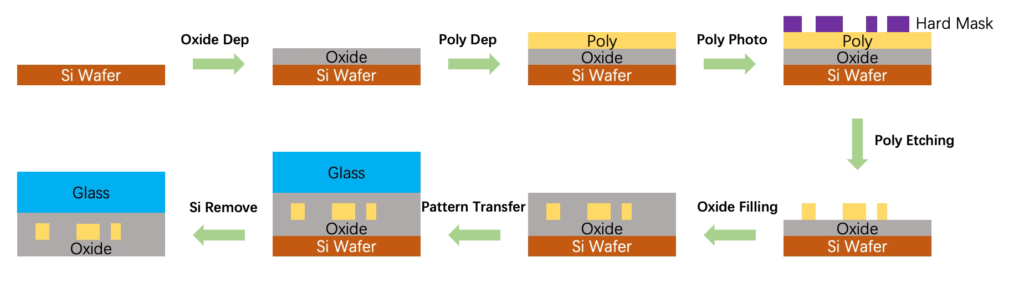
We have fully validated near-infrared products in mass production. Available wavelengths include 808 nm, 850 nm, 905 nm, and 940 nm, with compatibility for any waveform between 793 nm and 1000 nm. A platform for visible wavelengths is currently in development.
Please contact us with any questions you may have.